
Features
News
TLA celebrates 80 years of advancing innovation
A new logging formula among highlights of annual conference
March 27, 2025 By Andrew Snook

The Truck Loggers Associationโs (TLA) annual convention and trade show in Vancouver this past January marked a massive milestone for the organization. The TLA has been giving independent logging contractors throughout British Columbia a voice for 80 years, pushing for a healthier forestry sector while sharing information with loggers to help them improve their methods and bottom lines.
โThe TLA believes that a strong and sustainable working forest will generate long-term prosperity for the people of British Columbia, and that the people who work in our forests must share in that prosperity,โ said TLA president Dorian Uzzell, who is also a partner of Wahkash Contracting in Campbell River. โOur convention theme this year, โAdvancing innovation for 80 years,โ was chosen because loggers have been key innovators in the forest industry since the evolution of logging began in the 20th century. We have a long and successful history using modern technology to transform logging into data-driven, precise operations; boosting productivity and safety; reducing environmental impact and enhancing sustainability.โ
Uzzell acknowledged the uncertainty and challenges facing the forestry sector throughout B.C.
โThe entire sector is suffering, and that should not be a surprise to anyone who follows the industry,โ he told the crowd. โWhile the news of mill closures garners media attention, thereโs little said about the small, independent operators who employ a small number of people. These are our members who are downsizing and shutting down, and are the backbone of a healthy forest economy and the small rural communities of B.C. Policy that is being implemented is creating inefficiency, leading to the creation of uneconomical forests to operate in. And one has to wonder if perhaps this is the agenda of those opposed to forestry in B.C.โ
He stressed the need for the entire B.C. forestry sector to be operating in a healthy manner to ensure success.
โThe sector needs to be viewed as having a symbiotic relationship across the entire supply chain. Otherwise, instead of having the have and have-nots of the past, we will all become the have-nots,โ Uzzell said.
Premier Eby talks tariffs
One of the highlights of the conference was the Leaderโs Luncheon with keynote speaker Premier of British Columbia David Eby.
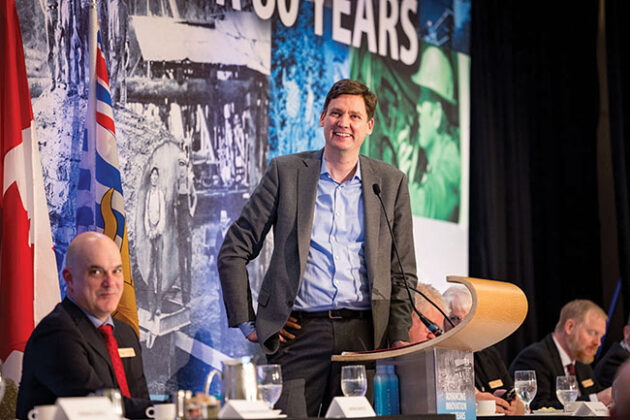
B.C. Premier David Eby was the keynote speaker at the Leaderโs Luncheon and offered the crowd a response to proposed U.S. tariffs.
The Premier offered the crowd a response to U.S. President Donald Trumpโs decision to apply 25-per cent tariffs on a wide variety of goods across Canada.
โFor our B.C. response, there are three components. One is that we will respond. Weโre standing shoulder to shoulder with Premiers across the country to say, โIf youโre going to do this to our families, youโre going to feel it, too.โ Weโre supporting retaliatory tariffs against key Republican districts in the United States to make sure that those decision makers understand the influence and impact of Canadian consumers on key products,โ he told the crowd.
Eby added that his government is also advocating that the federal government consider export taxes, or restriction on exports, of key commodities in a strategic way to minimize impact on B.C.โs economy and maximize the impact on key American districts.
The second component of the provinceโs response was of great interest to the crowd, which was strengthening the provincial economy by ensuring the acceleration of permit approvals to reduce bureaucratic delays in ensuring that resources are available, whether it is timber, metals, minerals, energy, or any other land-based activity. Eby added that provincial governments are also working on removing internal trade barriers across the country.
The third component of the provinceโs response to the new U.S. tariffs is diversification. Since many of the U.S. tariffs proposed are international in scope, other countries will also be looking for solutions, and Canada and B.C. can work together with those countries on those solutions, Eby said.
A formula for the future
An interesting panel discussion about how to keep forestry contractors sustainable with less than 50 per cent of the allowable annual cut included a presentation by Chris Duncan, MNP partner and national leader of forestry and forest products services. Duncan specializes in working with logging contractors, value added wood processors and various other forest-related businesses in B.C. and is a regular contributor to Truck LoggerBC magazine.
MNP was recently hired for a unique and challenging project: create an hourly rate for forestry equipment and then tie in productivity to that as part of a second phase. The project was originally announced two years ago at the TLA convention in 2023. The project was announced as a co-project between the TLA, the Interior Logging Association (ILA) and the North West Loggers Association (NWLA), and would be partially funded by the Government of B.C. MNP was awarded the contract in the fall of 2024.
โThe goal of the project is to support a balanced and transparent, trusting commercial relationship between contractors and licensees,โ Duncan told the crowd. โWhat weโre trying to do is create a model that will be a win-win for all parties involved, and weโll continue to make sure that the contracting business and the forest industry can be a thriving and profitable business for all parties involved.โ
The hourly rates will be based on validated capital and operating cost information, and then in Phase Two, will have productivity for a wide variety of equipment and processes that are used in the industry tied into the formula. The ultimate goal is to develop a dynamic and easy to use model that anyone in the industry can use, Duncan explained.
โItโs going to be an updatable database, so users will actually be able to input some of their own data to modify it, depending on the circumstances of their business and the productivity data is going to reflect a variety of situations and activities that are commonly experienced by contractors out in the field,โ he said.
The model will be able to be used in all regions of the province to create an estimate of a fair rate, which could then be used for the basis of future negotiations.
โThis will give everybody a starting point on negotiations to start talking when folks come to the table to determine logging rates,โ Duncan told the crowd.
MNP plans on creating the model through a collaborative approach where everyone thatโs involved in the industry has a part to play in the designing the rate model. To help build this model, MNP has formed an advisory committee with representatives from across the industry including logging contractors, contractor associations, the BC Council of Forest Industries (COFI), other licensees, and First Nations communities.
To help ensure the project has high-quality data, a random sample of contractors will be generated from a combination of TLA, ILA and NWLA member companies, as well as MNPs 400 contractors in forestry businesses across British Columbia.

MNP partner Chris Duncan discussed building a formula for an hourly rate for forestry equipment at the TLA Convention.
โWeโre building a random sample of contractors, so weโre not picking and choosing the contractors with the lowest numbers or the highest numbers. This is completely random chance, so that the accuracy of the data is that much stronger,โ Duncan said.
The project will involve collecting the administrative data on the equipment (what the contractors are experiencing) as well as drawing from the equipment manufacturersโ telematics data and the data that the equipment manufacturers have on historical operations of their equipment.
โThis will strengthen the financial data, because weโre using a variety of sources rather than just one source,โ Duncan said. โWeโre trying to remove any bias from the process.โ
After the initial rates are created, the model will require regular updating moving forward to ensure contractors have the most up-to-date data available to be able to pull from.
The project will be completed over two phases.
โWeโre currently in phase one, which is developing the model and the actual platform weโre going to use,โ Duncan said. โWeโve gone out and reached out to our first group of contractors that have been randomly selected to provide information. Weโre also having conversations with the equipment suppliers right now about telematics data and things like that. So ultimately, what weโre going to do in phase one will be building the industry list and selecting survey participants.โ
The next step is designing the hourly rate model for the equipment, taking the collected data and inputting it into the model.
โAfter that weโll be performing the validation of the rate model. So, that will be working with our advisory and working group panels to validate that the information that the model is giving us is actually accurate and usable,โ Duncan said.
They are currently in the process of doing the survey while also concurrently building the online platform in which the users will be able to retrieve the applicable rates from. The online platform will likely be made available through the three participating associations.
โTheyโll be accessible to their members, and then there will also be an Excel version that folks can put onto a laptop and take out where they want to, and a print version, which wonโt have the same power as the interactive model that the Excel or the web-based platform will have,โ Duncan said.
Phase one is expected to be completed by April 1, 2025. Once that goes live, the project will move into phase two, which is incorporating productivity. The second phase is expected to be complete by June 2026.
โProductivity has a lot more factors than just the equipment hourly operational costs. So, we will be taking a little bit more time on that part of the project,โ Duncan said.
He reiterated to the crowd that if they have received an email requesting their participation in the survey that they consider being part of the project.
โI canโt reiterate enough, answer the surveys that are coming out of that, if youโve gotten one. Weโre also doing some in-person interviews, if people arenโt as comfortable with computers,โ he said. โDeveloping the model, thatโs ongoing. Itโs all parallel to the survey. Weโre going to be moving into the validation process very quickly, and then weโll have the interface, and hopefully by April 1, there will be a model out there working that the associations will announce. And then weโll be moving into productivity, which weโll see a whole other group reached out to, as far as contractors to start building productivity data.โ
Print this page